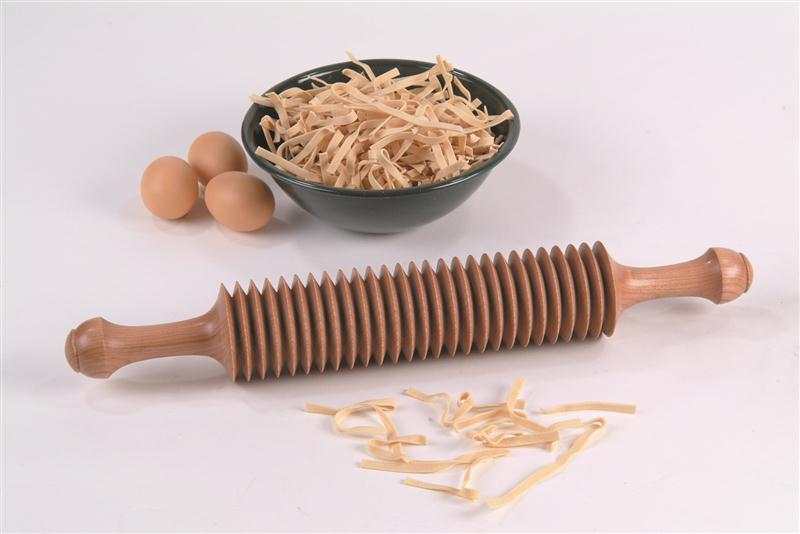
Bill Snelson is a pretty modest guy. “I started turning wood as a hobby about 30 years ago. I didn’t think it would go as far as it did when I started. I started selling things locally, and it went from there.”
What he doesn’t say is that he does all his turning work using traditional methods, and his wife, Gladys, works at his side, packing, shipping, tracking and helping with finishing.
Here at Lehman’s, we’re pleased to share the fruit of their labors with you. The most recognized piece the Snelsons make is the cherrywood noodle cutter. He also makes our:
- solid wood salt and pepper mills (Kidron store only, not online)
- French rolling pin
- solid cherry rolling pin
- laminated exotic wood rolling pin
Using only the best hardwoods sourced near his Western Maryland shop, the Snelsons send fresh shipments of artisan products to Lehman’s 9 to 11 times per year. “Years ago, I had the noodle cutter in the gift shop of a local restaurant. Mr. (Jay) Lehman was in there, and he spotted it. Eventually, we were able to make them for Lehman’s, and go into making the other things. That noodle cutter, though, that is popular out there in Ohio.”
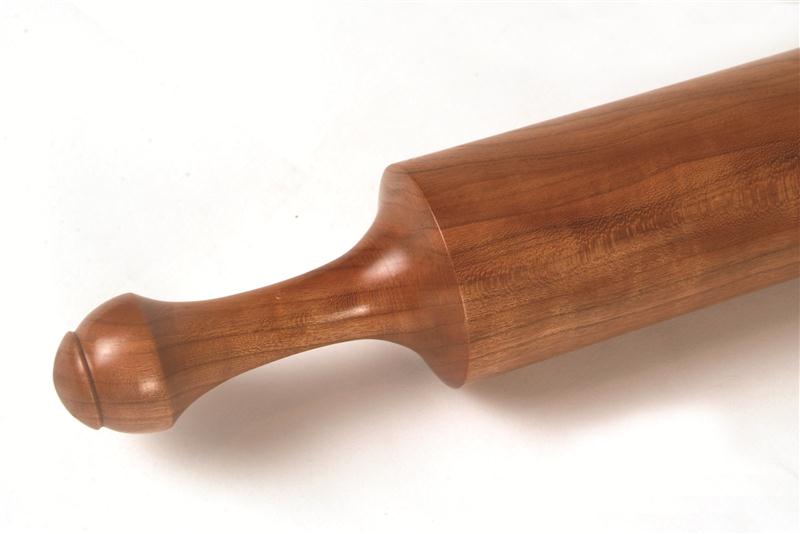
“They have to made by hand, you know, not on an automatic lathe, ” Snelson says. Each cutting row on the noodle cutter is laid out painstakingly. “I mark each one by hand. You can’t use a pattern on them, and you can’t turn them on big lathe. You have to mark them out, using calipers, by hand, and then shave each of the cutters down one at a time.” He uses a small electric lathe to individually turn each piece he makes, unlike the large, computerized ones used by mass-market makers.
Having spent 43 years working with his hands at the same Maryland brick factory, Bill Snelson appreciates good craftsmanship. “I started out moulding bricks, and eventually became a machinist, which I did 20 years before I retired. We made firebrick for steel plants, and you had to be very particular about the work. We made the best. Firebrick might not sound exciting, but it’s pretty important in a steel plant.”
He and his wife are equally particular about the turned wood items they produce. “The cherry wood comes from Pennsylvania. We turners and woodworkers say that the Pennsylvania cherry is the best in the country.”
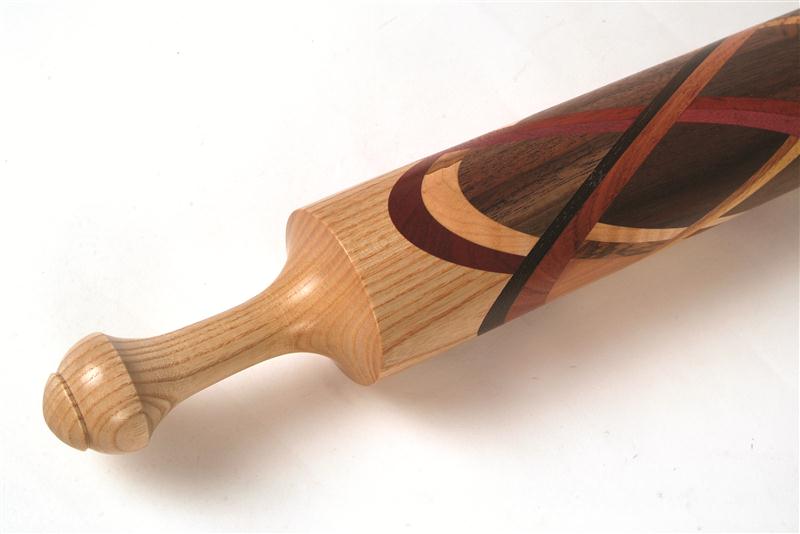
Many of the laminated pieces that he makes are created from exotic woods paired with American hardwoods. “I use cherry, walnut, curly maple, ash; purple heart, padauk, bloodwood, murado, yellow heart…We try to get as many colors in as we can on those laminated pieces, so they look nice, not like everything else out there. We cut and laminate the blocks by hand.” As he describes the lamination and gluing-up process, it’s easy to see that it could take a week or more for a laminated block to be ready to turn into a rolling pin or spice mill.
Since his retirement from the firebrick factory a few years back, Snelson says he has only one ‘real’ job now–keeping up with the demand for his turned wood items. “Sometimes, before I retired, it wasn’t unusual for me to do a 70 hour week. But now, it’s 30 hours, maybe a 40 hour week because we’re sending a shipment out.”
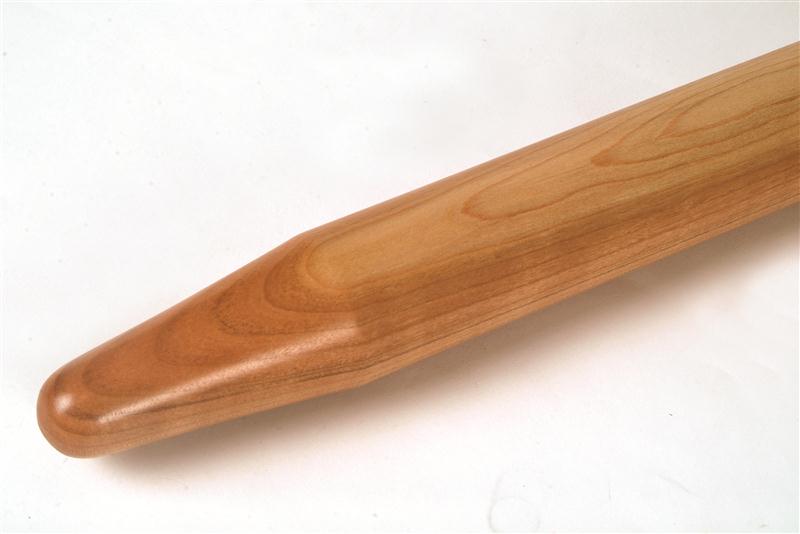
Each wood piece is hand finished. “I use what’s called a salad-bowl finish. It’s food-safe. There are three coats to put on, and each one takes about 24 hours to dry. I apply it with a foam brush right onto the item while it’s still on the lathe. Keeping the lathe turning a a steady speed is important, because that’s what keeps the finish even. We buff between the second and third coats, and then shine things up with a coat of beeswax after the third coat dries. Gladys, she helps me a lot with the finishing.”
He goes on to talk about his wife’s role: “She does all the packing and shipping, keeping track of all that. And she helps me keep the shop in order, and we do the finishing together. I couldn’t do it without her, that’s for sure.”
Click on the links above to see some examples of the items that Snelsons make for Lehman’s. We’re pleased to be able to share their craftsmanship and story with you.
Would love a noodle recipe to go along with the noodle cutter?